【FAトップインタビュー】シュナイダーエレクトリックに聞く 自社100工場超のDX実績を顧客へ還元「製造業向けDXサービス」製造業DX、スマートファクトリーへの道しるべ
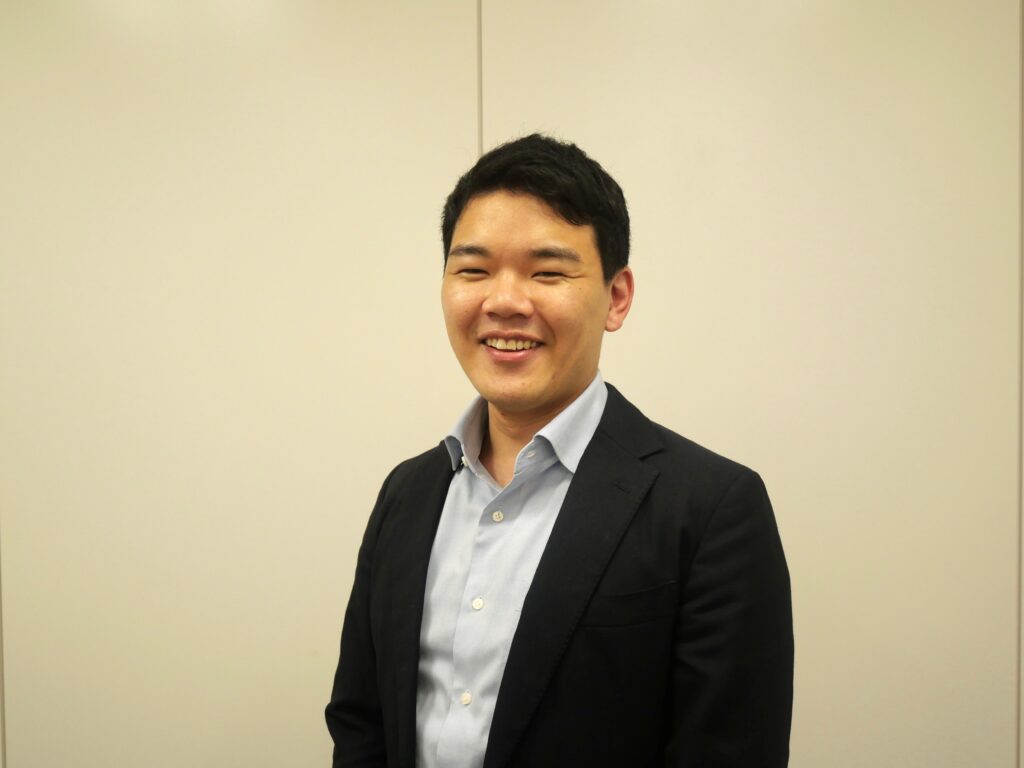
製造業は今、人手不足、熟練技術者の引退、多品種少量生産への対応、そして高騰するエネルギーコストといった、かつてないほどの複雑で困難な課題に直面している。こうした状況を打破すべく、多くの企業がスマートファクトリー化やDXの必要性を痛感しているが、「何から手をつければ良いのかわからない」「ツールを導入したものの、期待した成果が出ない」といった声が聞かれるのも事実だ。
それに対しシュナイダーエレクトリックは、自社の巨大なサプライチェーン改革で培った膨大な知見と実績をもとに、製造業各社のDXの線略策定から実装、運用まで一貫体制で支援する「製造業向けDXサービス」を開始した。同サービスについて、インダストリアルオートメーション事業部 商品企画部 DXサービス担当 門倉 慧太 氏に聞いた。
イチから製造業のDX実現をサポートするサービス
――製造業向けDXサービスについて、その概要を教えてください
このサービスはある特定の製品を売ることを目的としたものではなく、お客様のDXにおいて「どこに課題があるのか」「目指すべき姿はどこか」を共に探求することから始まります。現状と目標との間に存在するギャップを明確にし、そのギャップを埋めるための具体的な施策を定義する。いわゆるコンサルティングやアセスメントというアプローチでお客様を支援するサービスです。そこで描いたロードマップに基づき、当社の様々な製品やパートナーのソリューションを活用してDXを実現していくところまで責任を持ってサポートします。
2017年から巨大なグローバルサプライチェーン改革を実践
――なぜメーカーである御社が、コンサルティングのようなサービスまで手がけるのでしょうか?
背景には、私たち自身が巨大なサプライチェーンを持つ「ものづくり企業」であるという事実があります。当社は日々、お客様から15万点以上のオーダーをいただき、29万点以上の商品を扱っています。これらを生産するために世界44カ国に153の工場を持ち、20,000社以上のサプライヤー様と取引をしています。全従業員約15万人のうち、約半数にあたる約8万人が、このグローバルサプライチェーンに携わっています。
この非常に巨大で複雑なサプライチェーンを効率的に運営していくためには、DX、つまりデータの連携やプロセスの効率化が不可欠です。そこで2017年から、全社的にスマートファクトリー、スマート物流センターを構築するプログラムを開始したのです。
――自社が抱える課題を解決するためにDXに取り組まれたわけですね。
その通りです。優先的にDXに取り組む工場を選定し、様々な施策を投入していきました。その過程で、DXを成功させるための独自の方法論、いわば「シュナイダー流のDXルール」を構築し、それをテコに加速度的にスマートファクトリーを増やしていきました。現在では100カ所以上のスマートファクトリーとスマート物流センターを運用しています。
――100カ所以上とはすごい数ですね。具体的にどのような成果が出ているのでしょうか。
私たちが定義する「スマート」とは、単にデジタルツールを入れることではありません。必ず具体的な成果に結びつけることを重視しています。例えば、省エネ効果では電力使用量を10%~12%削減すること、工場の生産性では年間5%~10%の改善を行うことなどを目標に掲げ、実際に達成しています。多くの施策は、1.5年から3年程度での投資回収を目安としています。
こうした実績は外部機関からも高く評価されており、特に世界経済フォーラムが先進技術を導入・活用している工場を選出する「lighthouse(ライトハウス)」には、現在、7工場が11選定受けています。
DXを成功に導く「3つのルール」と「全社的ガバナンス」
――「シュナイダー流のDXルール」について詳しく教えてください
各工場がバラバラにDXを進めても、全社最適には繋がりません。そこで私たちは、スマートファクトリーを定義するために、大きく3つのルールを設けています。
1つ目は「SPS(Schneider Performance System)」です。これは元々トヨタ生産方式(TPS)をベースにしたもので、生産性や品質、設備保全などに関する非常に細かい項目をスコアリングし、1200満点中720点以上で「スマート」と認定します。このスコアは工場長のKPIにも紐づいており、給与にも直結する仕組みで、本気で改善に取り組む文化を醸成しています。
2つ目は「MMR(Minimum Mandatory Requirement)」。これは導入すべきITシステムを定めたもので、例えばSCADA(監視制御システム)はこの製品を使いましょうといった指針です。「スマート」と呼ばれるには、ここで指定されたシステムを100%導入し、かつ稼働率が80%以上であることが求められます。
3つ目は「DQAI(Digital Quality Assessment Indicator)」という品質に関する指標です。品質が維持されているか、そしてその管理にデジタルがきちんと活用されているかを評価し、スコアが75%以上であることを条件としています。
――非常に明確な基準で、それを徹底させる仕組みも素晴らしいですね。
ルールを機能させるための組織体制も構築しています。グローバルサプライチェーンのトップを「スポンサー」とし、その下に全世界の工場を統括する責任者や、IoTやAGVなど各技術分野の専門家をグローバルに配置しています。そして各工場にはスマート化を推進するリーダーがいます。この強固な組織体制でガバナンスを効かせることで、全社として最適なDXを推進できるのです。
日本でもサービスをスタート 顧客の反響とサービスの強み
――自社での実績と方法論を顧客向けにサービスとして提供し始めたわけですね。
自社の取り組みをお客様に説明する中で、「シュナイダーはどうやってDXを成功させたのか教えてほしい」というお声を非常に多くいただくようになりました。そこで、私たちが長年蓄積してきた知見をお客様に提供しよう、というのがこのサービスの始まりです。海外では2023年頃から組織的に展開し、日本では2024年から正式にサービスとして開始しました。
――コンサルティングファームや他の大手メーカーとの違いや強みはどこにありますか?
他社との違いは明確です。いわゆるコンサルティングファームとの違いは、私たちが「現場を知る実践者」である点です。机上の空論ではなく、自社工場で汗を流し、試行錯誤を繰り返してきた経験に基づいた、非常に泥臭く、現実的なご提案ができます。「言葉だけでなく、私たちの工場を実際に見に来てください」と言えるのは、メーカーである私たちならではの強みです。
他のメーカーとの違いは「ソリューションありきで走らない」点です。私たちはまず、お客様の経営課題に寄り添い、どこにゴールを置くべきかという戦略やロードマップを共に描くことから始めます。その上で、最適なソリューションは何かを考えていく。この「戦略策定から実装・運用まで一気通貫でサポートできる」ハイブリッドな立ち位置が、私たちの最大の価値だと考えています。
――お客様の反響はいかがですか。
予想以上の引き合いをいただいています。サービス開始からまだ日は浅いですが、既にお問い合わせは多数あり、実際にアセスメントやロードマップ策定を進めているお客様もいます。中には、パイロット導入のフェーズに入ろうとしているお客様も出てきています。特に、組立製造業のお客様や、食品・薬品といった一般消費財を扱うお客様からの関心が高いと感じています。
なぜ今、スマートファクトリーなのか?
――今、改めてスマートファクトリーやDXが注目されている背景には、何があるのでしょう
以前は「できたらいいね」という、いわばプラスアルファの取り組みだったスマートファクトリーが、今は企業の存続に直結する「経営課題」そのものになったと感じています。熟練技術者がどんどん引退し、技術伝承が間に合わない。人手不足は深刻化し、人件費は高騰する。お客様のニーズは多様化し、多品種少量生産への対応は待ったなしです。こうした課題を解決するためには、もはやDXは避けて通れない道になっています。
また、AIや5Gといった技術が成熟し、かつては不可能だったデータ活用や分析が現実的になったことも大きな要因です。
「これまで自社でExcelを駆使したり、内製のシステムで何とか対応してきたけれど、いよいよ限界が来た」「とりあえずロボットやITツールを入れてみたけれど、部分最適に終わり、思うような成果に繋がらなかった」そうした方々が「やはり全体を俯瞰して、戦略的に進める必要がある」と気づき、外部の専門的な知見を求めて私たちにお声がけいただくケースが増えています。
私たちは、お客様の工場を「6つの領域(①運用効率と品質、②設備管理、③エネルギー管理、④データ管理とAI、⑤サイバーセキュリティ、⑥ガバナンスとチェンジマネジメント)」で評価し、どこに真の課題があるかを可視化します。特に最後の「ガバナンスとチェンジマネジメント」、つまり「導入して満足」で終わらせず、現場が使いこなし、成果を出し続ける仕組みをどう作るか、という点が最も重要であり、私たちのノウハウが最も活きる部分です。
――今後に向けて
多くの日本企業がDXの必要性を感じながらも、その第一歩をどこから踏み出せばいいか、悩んでいると思います。私たちは、自らがそれを乗り越えてきた実践者として、その難しさも成功の秘訣も知っています。
私たちのサービスは、ただレポートを書いて終わりではありません。お客様の工場に足を運び、現場の方々と対話し、共に汗をかく。「戦略」と「現場」の両輪を動かし、具体的な成果が出るまで伴走するパートナーです。私たちのライトハウス工場をご覧いただくだけでも結構です。そこで工場の未来を拓くヒントを見つけてもらえればと思っています。https://www.se.com/jp/ja/work/services/consulting/industrial-digital-transformation/
