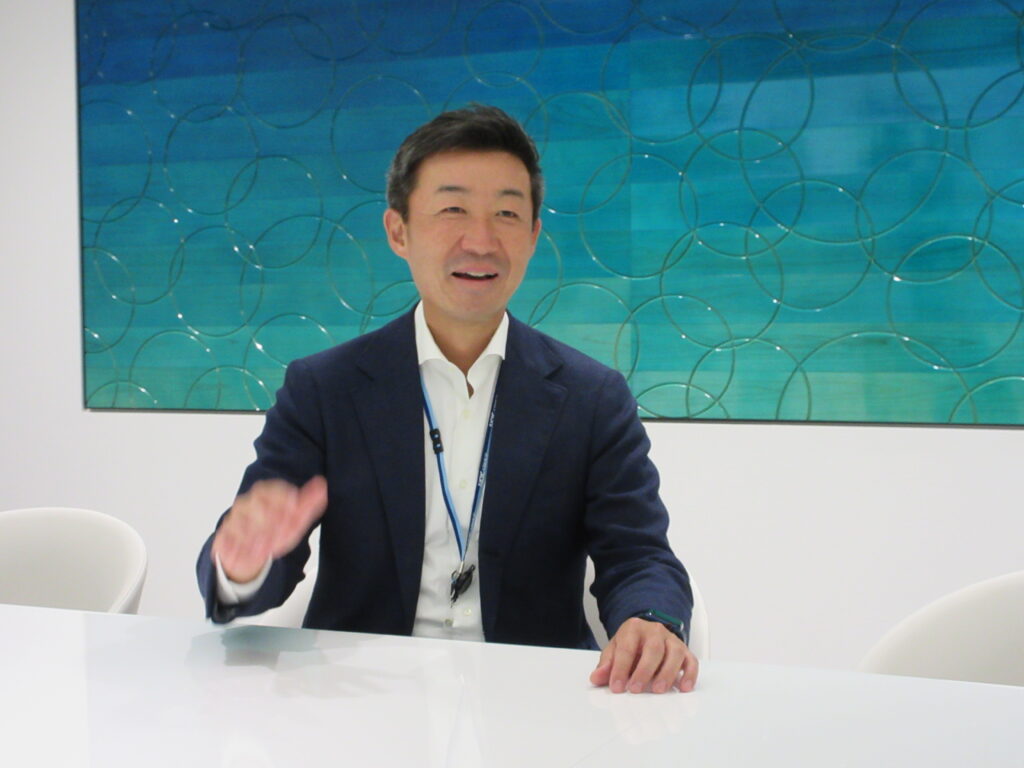
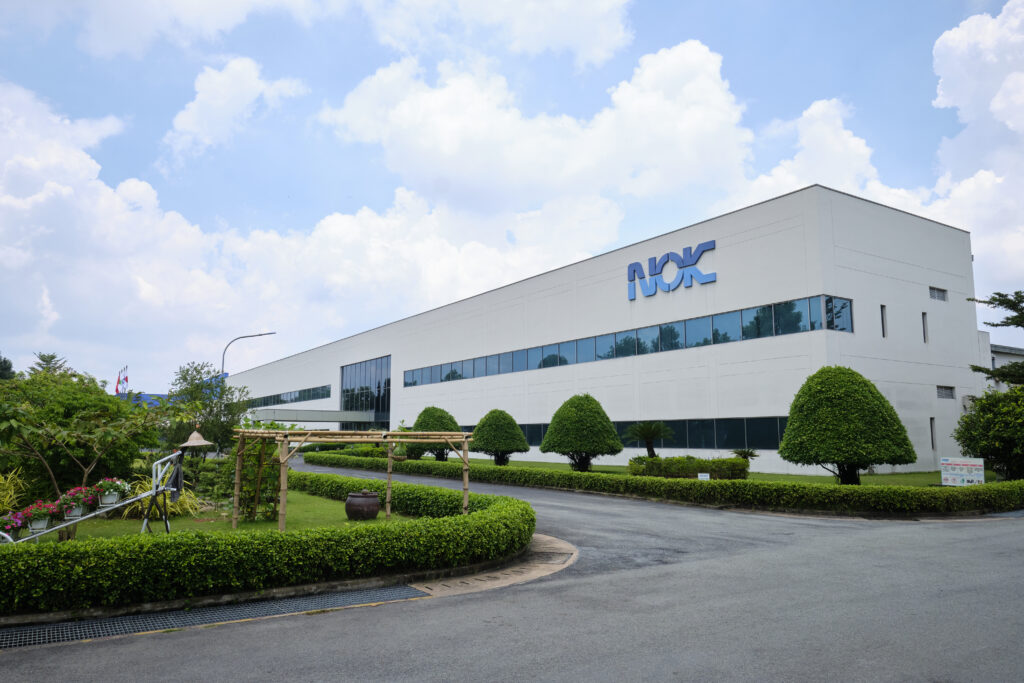
工場の形は各社それぞれ。何を重視し、こだわるかは各社で異なり、そこに正解はない。だからこそ、将来どんな工場にして何を得たいか、そこに向けてどう進化させていくか、自社の理念と明確な軸を持つことが大切だ。
オイルシールやOリングの世界トップメーカーのNOKは、2022年7月にベトナム工場で新たにOリング生産棟を増築して稼働を開始。「品質」と「人を尊重する」という同社の経営理念がよく現れた工場となっている。NOK 取締役 専務執行役員 事業推進本部長 折田純一氏に話を聞いた。
自動車やロボットなど世界的に需要拡大が続くOリング
Q.ベトナム工場の生産品とその位置付けを教えてください。
折田氏 ベトナム工場ではOリングとオイルシールを製造し、生産したものの78%を日本へ輸出しています。日本の自動車メーカーや自動車関連業界のお客様向けとなり、高い品質レベルが求められるため、日本国内の主要拠点である福島・熊本工場の技術を持ち込んで、高い生産品質を実現しています。
ASEANではインドネシアやタイにも工場はありますが、そちらは現地向けの日系自動車メーカーや現地OEM向けになっています。
Q.Oリング、オイルシールの需要は増えているのですか?
折田氏 そうですね、ハイブリッドやEVなど電動車を軸に世界的にモビリティ需要が拡大していることに加え、コロナ禍によって感染リスクの低い自動車が安全な移動空間として再認識されたことも大きいと思います。半導体不足も緩和に向かっていて、今後も自動車のニーズは増加し、それにともなってOリング・オイルシールも必要数が増えると見込まれています。
また産業用ロボットや協働ロボットなど自動化にともなう産業機器で使われる数も増えています。
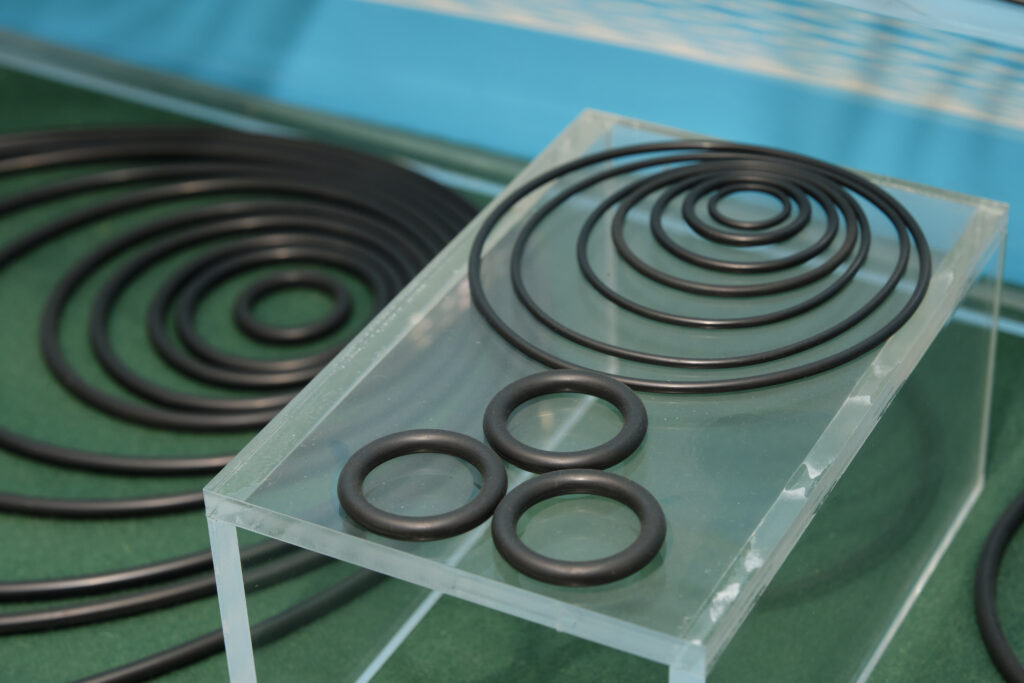
増築の目的は生産能力増強とサプライチェーンの強靭化
Q.今回の増築は、Oリングの需要増に備えた生産能力強化という認識で良いですか?
折田氏 Oリングの需要増はもちろんですが、日本からの生産分散とサプライチェーンの分断を阻止したいというのが今回の増築の狙いです。
現在、Oリングの生産は、日本国内が60%を占めています。しかし近ごろ国内では、地震や台風、大雨などの自然災害が多発しています。2016年の熊本地震では当社の熊本工場も被災しました。当時、生産の一時停止を強いられたこともあり、生産拠点を分散する必要性が高まっていました。
また、新型コロナウイルスの感染拡大によって世界規模でサプライチェーンが影響を受けました。当社は従業員の頑張りに助けられてなんとか安定供給を死守できましたが、サプライチェーン分断のリスク回避も課題でした。
そうした背景があり、ベトナムは生産拠点として非常に優れていることから増築の判断に至りました。
ベトナムは人口の平均年齢が30.1歳ほどと若く、多くが親日的で勤勉、手先も器用です。ASEANのなかでも比較的賃金が安く、労働力を確保しやすい。経済成長の伸びも著しく、政治的・経済的に安定し、日本との関係も良好というのも大きな後押しになりました。
品質向上に向けて製造工程のデータを電子化して診える化
Q.ベトナム工場はどれくらいの規模なのですか?
折田氏 ベトナム工場は、ベトナム南部、ホーチミン市の北のドンナイ省ビエンホア市のアマタ工業団地内にあります。約9万5000平方メートルの敷地に2万平方メートルのオイルシール棟、1万2000平方メートルのOリング棟で構成され、1994人の従業員が働いています。年間のOリング生産能力は約3.6億個となっています。
今回のOリング生産棟の増築部分は、既存の生産棟と同じ1万2000平方メートルあり、広さが約2倍になりました。従業員も新たに約400人を採用する計画で、生産能力も約6億個へと大きく増加する見通しです。
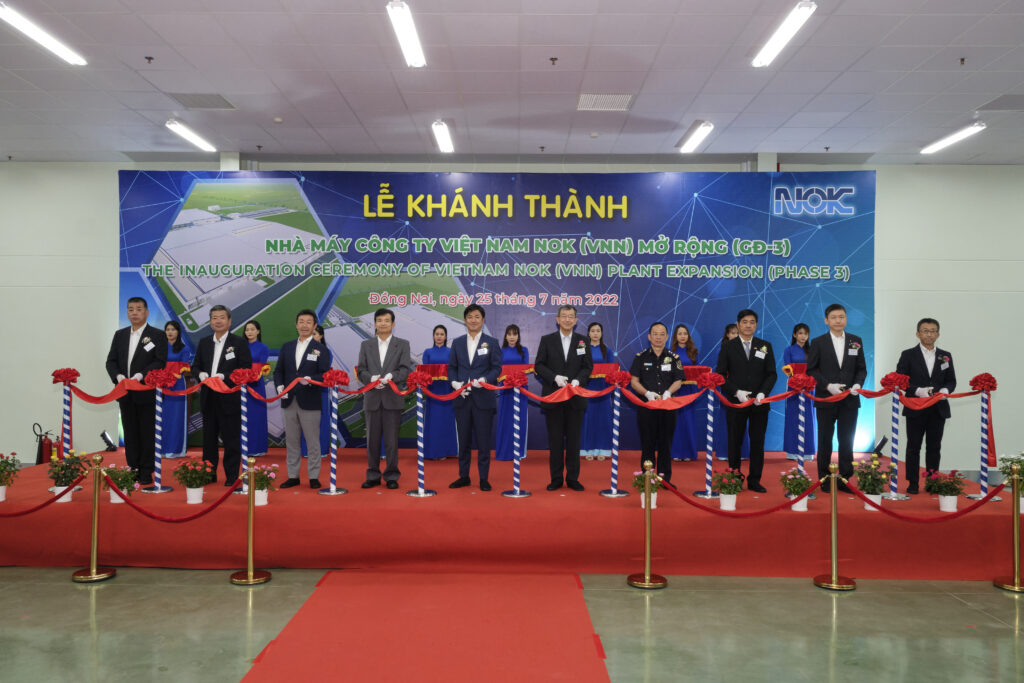
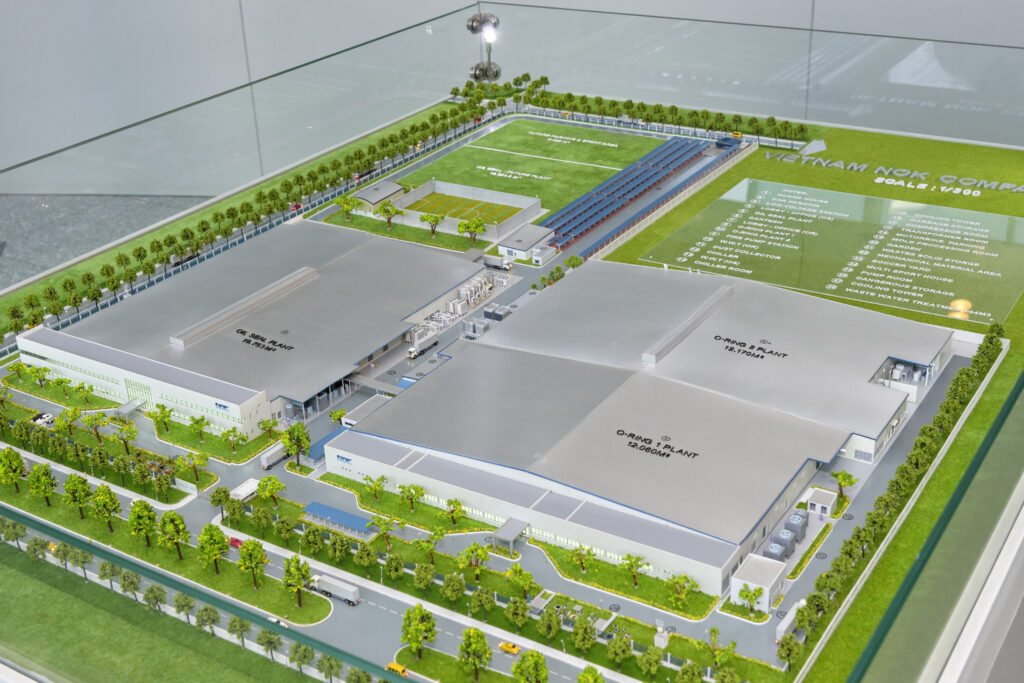
Q.今回、ベトナム工場で実現した新たな取り組み、力を入れた部分を教えて下さい。
折田氏 今回、特に力を入れて取り組んだところは2つあります。製造面では工程データのデジタル化による業務効率化と品質向上、従業員の働きやすさ向上と管理業務の効率化として食堂や駐車場管理のスマート化です。
製造面では、スマートインフォメーション(デジタル診える化)を推進し、工程データと検査データを電子化し、それを統合管理することで、早期の異常発見と対策、トレーサビリティを強化しました。
各工程のデータを接続して一元管理し、製造ラインの目標個数や進捗、生産実績、不良発生数などがいつでも確認でき、現場マネージャーはタブレットでも見られるようになっています。検査の抜け漏れを防ぎ、不良が見つかったら、そこからドリルダウンして、どのロットで、どの工程のどこに問題があったかを素早く突き止め、対策を打つこともできます。昔は紙でやっていたため、分析や対応に時間がかかりましたが、いまは状況をリアルタイムにモニタリングして迅速に対応できます。
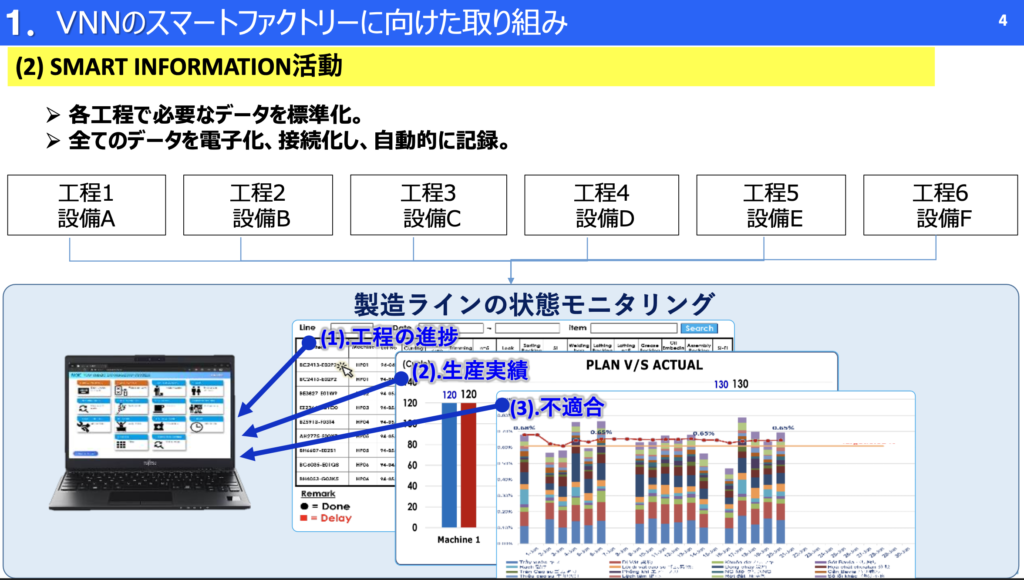
Q.効果のほどはいかがですか?
折田氏 今回は、製造(製造ラインの電子化)、品質管理(検査記録の電子化、異常処置ルートの電子化(試験・抜き取りプロセスの電子化)、型管理(型管理・洗浄プロセス管理)、部品準備(準備工程内の電子化、型管理・払出・使用状況管理)、出荷倉庫(入庫・出荷プロセス管理)、原材料管理、人事(人員・給与・明細書のオンライン化、食堂サービスの電子化、駐車場管理システムの電子化)をデジタル化して見える化しましたが、各業務で生産性が25%アップし、紙の使用量も50%以上減らすことができました。また異常の早期発見やトレーサビリティ強化、各種データの検索時間短縮といった定性的な効果もありました。
従業員の働きやすさ&フードロス削減につながった食堂のスマート化
Q.もうひとつの取り組みが食堂や駐車場の管理システムということですが、スマートファクトリーやDX、デジタル化の文脈では意外な気がしました。
折田氏 当社は「人を尊重する」ことに重きを置いており、従業員にとって食堂はとても大切な場所です。お腹が減ったら元気は出ませんし、美味しいごはんを食べれば頑張ろうと思えますよね。東南アジアは若い人が多く、ベトナム工場で働いている人たちも若くてよく食べます。社員に気持ちよく働いてもらうためには、食堂の充実はとても重要なのです。
Q.確かに。具体的にはどんな形にしたのですか?
折田氏 食堂のメニューを電子化し、スマートフォンで事前に注文する仕組みにしました。
以前から昼休みの食堂はとても混雑していました。人気のあるメニューには長い行列ができ、時には一部のメニューが売り切れになることもありました。特にコロナ禍の3密防止下では、グループ分けをして食堂の利用時間をずらしていたので、順番が遅いグループになると注文できるメニューが限られ、不平等になってしまうという問題がありました。
そうしたことをなくすためにシステム化を行い、3日前までにスマートフォンでメニューを申し込んでおけば、昼休みに食堂に行って指紋認証をすると注文済みのメニューがすぐに出てくるようにしました。
Q.これは嬉しいですね。確かに行列に並ぶのはストレスです。
折田氏 お昼休みの時間は限られています。そのなかで行列に並ぶのは嫌ですし、ましてや食べたいものが食べられなかったらガッカリします。新しいシステムは、列に並んで待つことなくスムーズに食事を受け取り、昼休みの時間を長く使えるととても好評です。
またそれだけでなく、フードロス対策にも大きな効果を上げています。
以前は食材の余剰だったり欠品が出るのが当たり前でした。次の日に回せる食材もあれば、当日に消化しなければならない食材もあり、なかなかフードロスを減らすことが難しかったのです。しかし今は予約注文制なので過剰な仕入れも廃棄も減らすことができました。
この食堂管理と運営の仕組みは、日本でもまだ導入しておらず、ベトナムで世界に先駆けて導入しました。
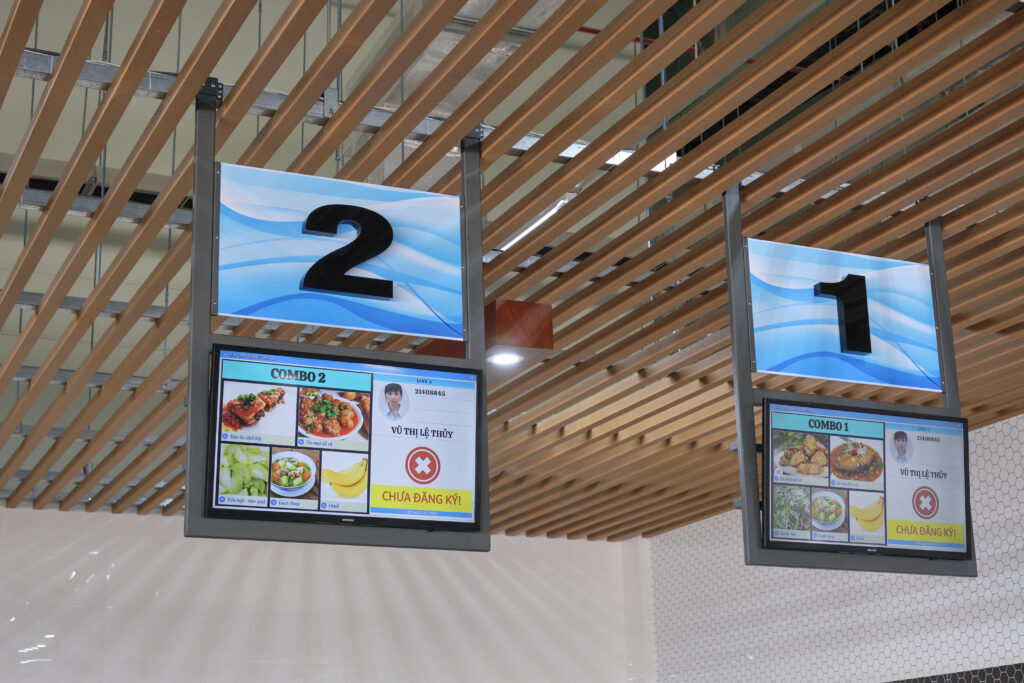
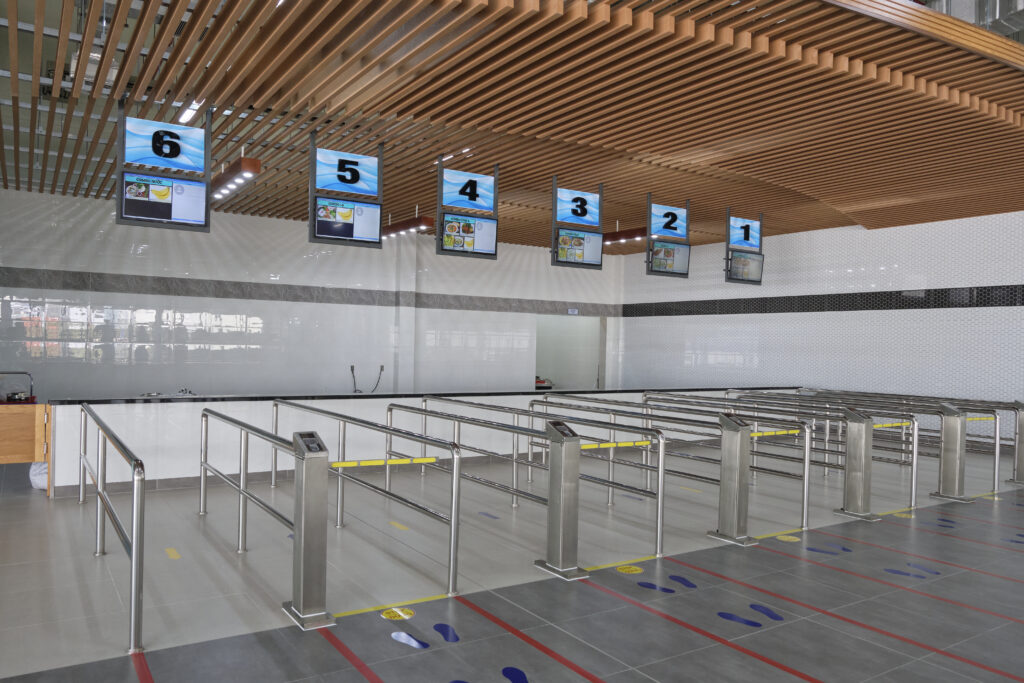
駐車場管理システムも一新 入退勤時の混雑を緩和
Q.従業員満足とフードロス対策の一石二鳥ですね。駐車場の管理はどのようなことを行ったのですか?
折田氏 駐車場に顔認証システムを導入し、入出庫管理を効率化し、不審者の入場も防いでいます。
ベトナムはバイク通勤が主流で、何百人もの従業員が一斉にバイクで通勤してきます。これまで駐車場の入口では、複数名の守衛さんが、出勤してきた従業員の顔と社員証を確認し、紙の駐車チケットを手渡しして入出庫管理をしていていました。やはりここでも食堂同様、毎日長い行列ができていました。
Q.それも従業員にとってはストレスになりますね。音や排気ガスも酷そうです。
折田氏 その通りです。ですので、それを解消するためにシステム化しました。
駐車場の入口にカメラを2台取り付け、顔認証とナンバープレートを撮影し、管理システムのデータを照合。問題なければそのまま入場、他人だったりナンバーが違っていたら入場できないという自動化の仕組みにしました。これによって入退場がスムーズになり、管理のための守衛さんの人数も抑えられ、セキュリティを高めることもできました。
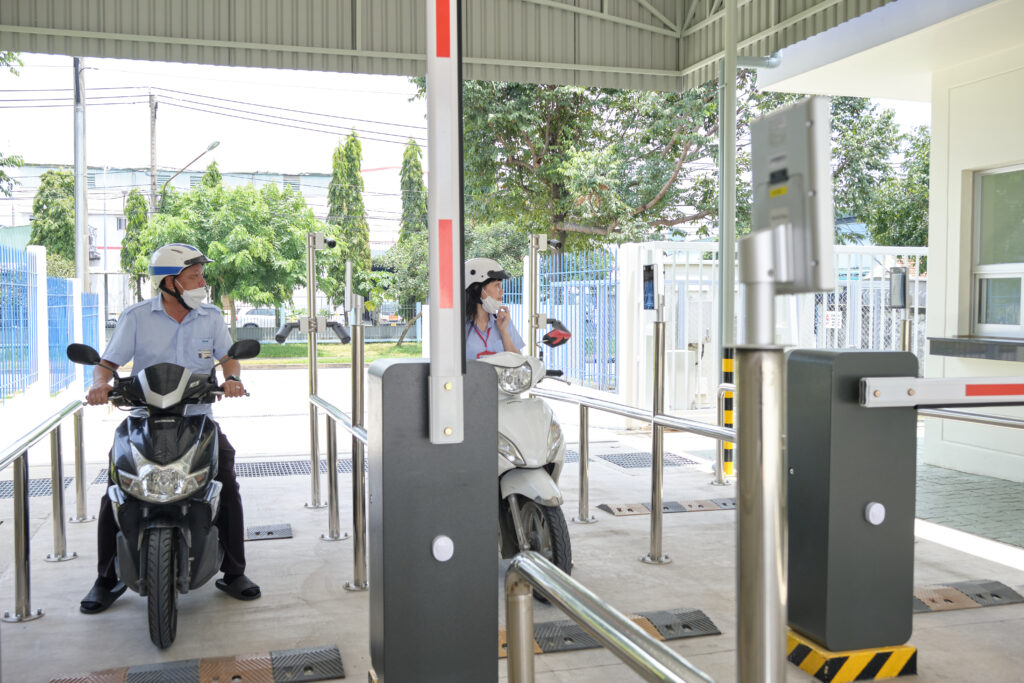
品質と人尊重に軸足を置くNOKのスマートファクトリー
Q.スマートファクトリーというと、自動化やロボット、AI導入などを通じて生産性向上を主眼としたり、脱炭素に向けたカーボンニュートラルに向けた取り組みが目立ちます。御社のスマートファクトリーの取り組み、方向性について教えてください。
折田氏 当社のスマートファクトリーは、ダントツの品質と、人と環境にやさしいものづくりをポイントに進めています。
ダントツの品質とは、製造情報を収集して、集約、分析して見える化を行い、当社がこれまで培ってきた技術に裏打ちされた高品質の製品を作ることを言い、不適合なものは徹底的にトレーサビリティを行って改善をしています。
Oリングやオイルシールはもう数十年以上作っていて、基本的な作り方は完成しています。しかしながら車の性能が上がるにつれ、Oリングにかかる圧力が高くなっていたり、漏れに対して敏感になっていたりするので、私たちは常に品質を高めていく努力を続けていかなければなりません。基本的な作り方は同じでも品質を高めていくため、検査をより緻密に行うようにするなどの工夫を重ねています。
人にやさしいに関しては、経営方針に「人間尊重」を掲げ、以前から人を大事にすることを重視してきました。人間に負荷がかかる工程はなるべく自動化していこうという考え方で進めています。
生産性向上に向けて現場改善に積極的に取り組んでいますが、効率や損益だけ考えて、改善して原価が下がったけど従業員は大変になったというのは改善ではありません。改善は、現場の人が喜ぶ改善でなければいけないものです。自動化・オートメーション化は従業員にとっては負荷を下げるものであり、そうして空いた時間を品質や付加価値の高い仕事へシフトしてもらう。こうした哲学で進めています。
人は間違いを起こすもので、現場で働く人はそのプレッシャーに囲まれており、それを減らすことも大切。現場で働いている人のストレスを解消し、新たなストレスをかけないことが最終的には自社の利益につながると考えており、そこに向けて取り組んでいます。
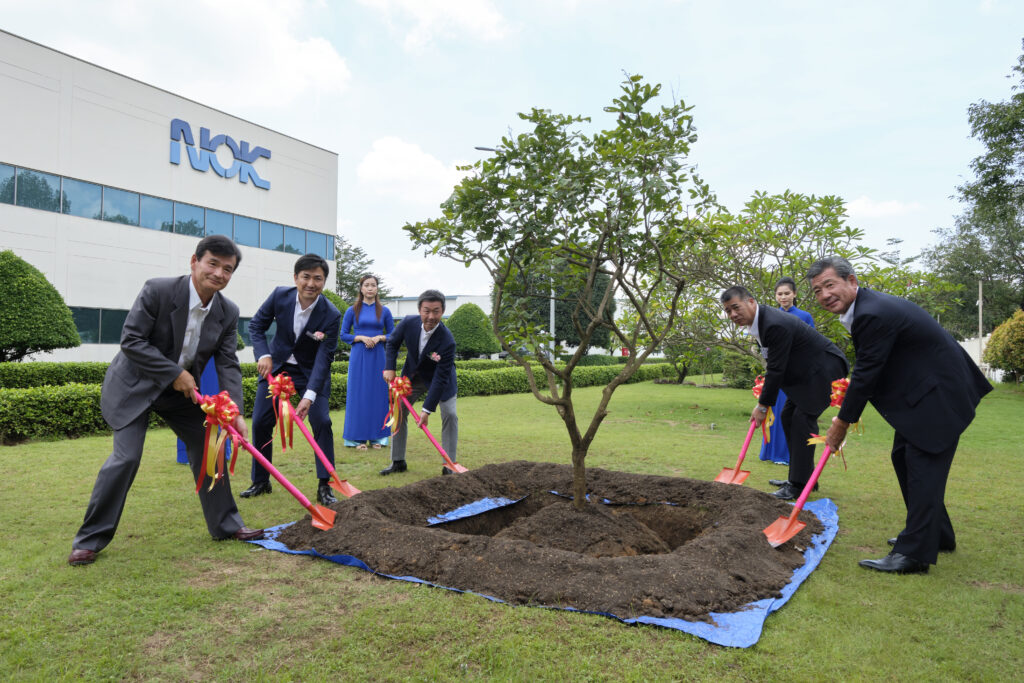
Q.今後に向けて
折田氏 海外工場では日本の国内工場で確立した機械・設備で運用しており、従業員の賃金も年々上昇しています。そのなかで収益性を高めるには、日本国内の生産技術力を強化することが不可欠です。
現在は後工程の自動化に取り組んでいます。例えばOリングは、ふにゃふにゃと柔らかく、ロボットでは掴むのが難しいため海外では人手作業が中心ですが、国内ではロボットによる自動化を進めています。すでに生産ラインに導入して実践しています。
また今の後工程の機械は、大型で、ある工程専用機になり、高額で稼働開始までのリードタイムが長くなっているという課題があります。もっとシンプルでスマート、小さくし、且つ汎用的にして、スペースあたりの生産性を高めるような機械にしたいと考えています。そのためにはロボットをはじめ、カメラや画像処理、AIの技術等がカギになり、それを使いこなし、実現するためにも生産技術のさらなるレベルアップは重要だと考えています。
人が介在せず、素材を投入したらそのままものが完成する。将来的にはそうしたスマートファクトリー的な、モデルファクトリーも作ってみたいですね(笑)。
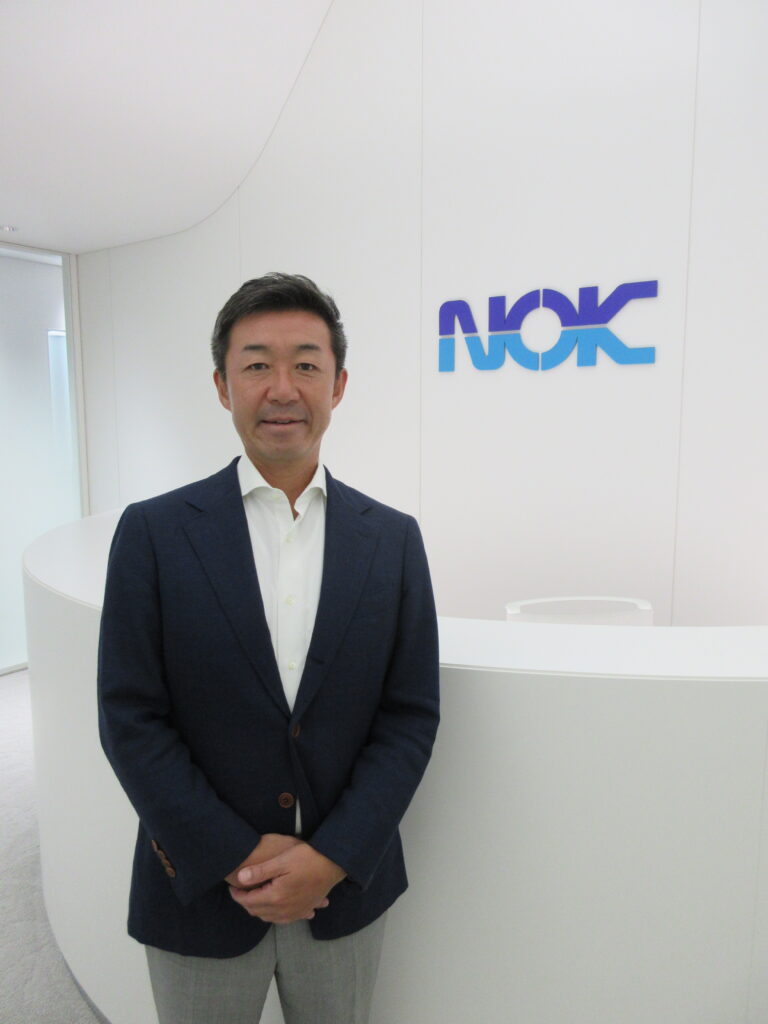
【NOKベトナム工場の概要】
社名:Vietnam NOK Co., Ltd.
設立:2004年8月4日
主要生産品目:Oリング、オイルシール
従業員数:1994名 (22年3月末時点)
資本金:2700万USドル(約30億円)
土地面積:アマタ工業団地内 9万5000平方メートル
建物面積:4万4000平方メートル
・オイルシール棟2万平方メートル
・Oリング棟1万2000平方メートル
・Oリング棟増築分1万2000平方メートル