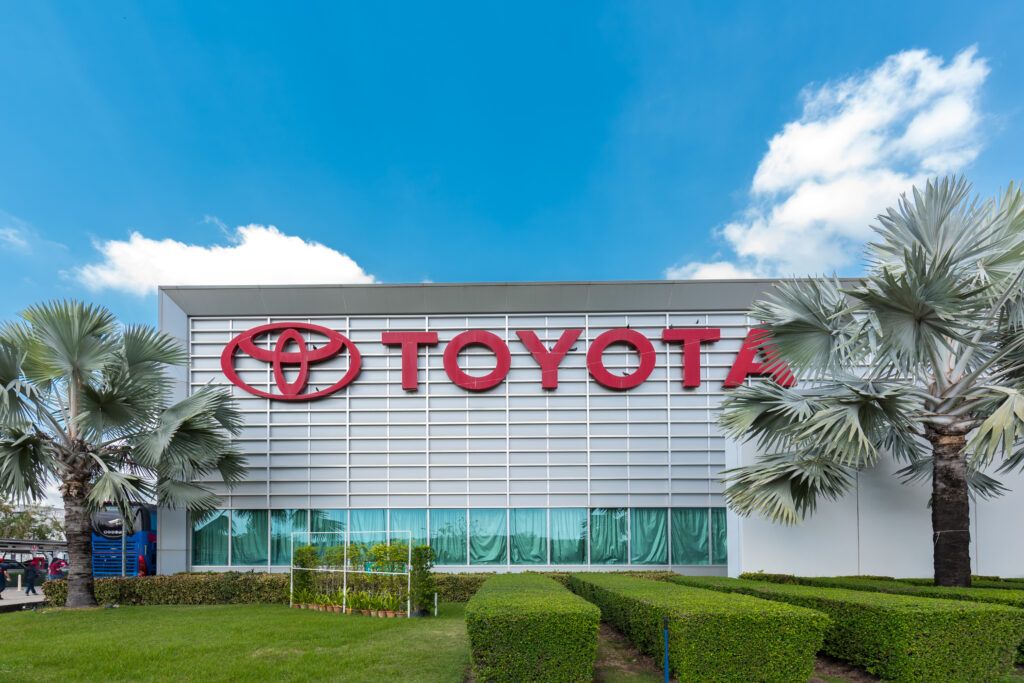
いまや自動車は走る電子機器と言っても過言ではなく、さらにEVやコネクテッドカー、自動運転によって電子化の流れは加速しています。この流れのなかで、品質に対する考え方にも変化があり、電子化に伴って重要性が高まっているのが、はんだと電子部品の実装品質です。
トヨタ自動車は、2021年に新たに作成したトヨタ技術標準(TSC)で、はんだ外観基準について、はんだと実装技術の国際品質標準であるIPCを正式に採用。それまでの社内基準からIPCを核とした新しいはんだ外観基準を作り上げました。その目的と背景、狙いについて、トヨタ自動車株式会社
制御電子システム開発部 開発プロセス・品質改革室 石川 昌広氏と、電子性能開発室 西森 久雄氏に話を聞きました。
社内基準にIPCを採用するまでの経緯
――おふたりの社内での役割について教えてください
私たち2人はトヨタ社内では設計側の立場となります。私(石川)は、設計品質全般を見ており、その立場で”はんだの外観基準”の社内基準を作って発行しております。西森は電子部品の評価品質を開発している部署にあり、”はんだの耐久試験”の試験法を開発している立場になります。
一方で、はんだの製造品質も重要項目なため、トヨタでは、”はんだの製造品質”は、品質保証部が管轄して見ています。
今回は、設計や部品評価の立場から管理をしている、「はんだ付けの品質に関わる外観基準」の話として聞いていただけると良いと思います。
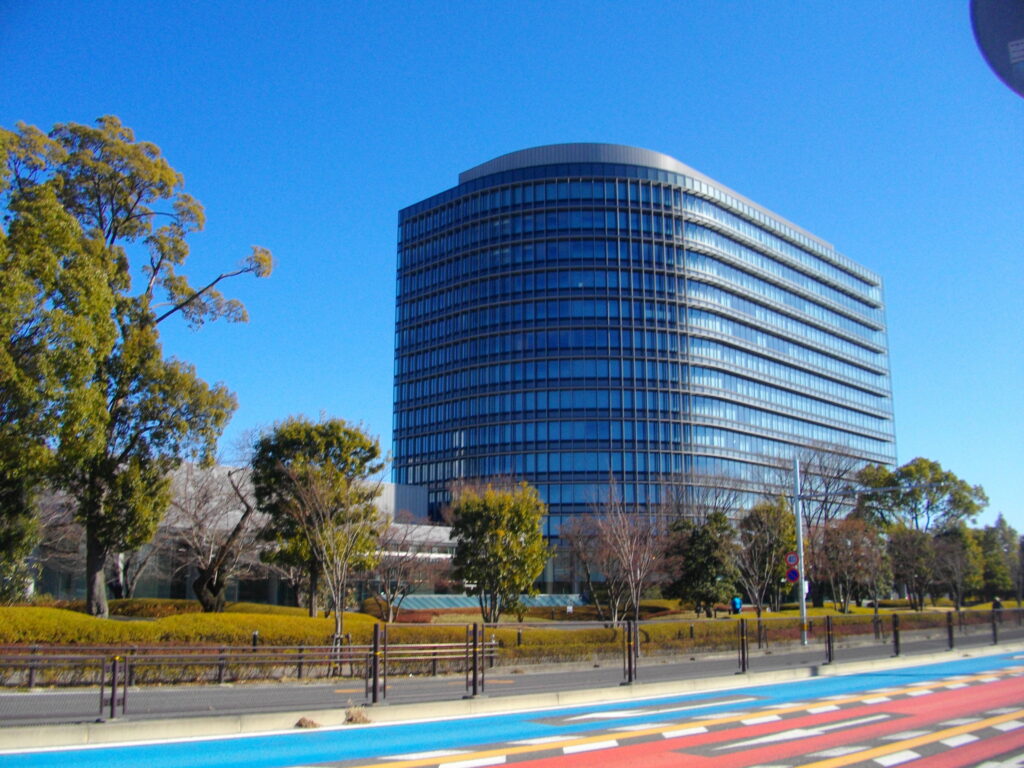
――これまではんだの品質確保はどのように行われていたのですか
はんだ付けは、品質における信頼性の重要なポイントと認識していて、30年以上前からトヨタの社内基準を持っています。それを逐次改訂しながら、はんだに対する信頼性、設計品質を担保してきました。
一方、外注設計と言って、ティア1に対して要求仕様を発行し、それを元に開発・納入していただく製品もあります。その場合、ティア1に対して、はんだの製造品質を確認するのは、品質保証部が行い、海外では海外の工場品管が主に行なっています。
はんだの品質確保については、設計段階からの信頼性と製造品質の2本の柱があり、そのトータルでこれまでの品質を確保してきました。
しかし、車両販売や製造拠点がグローバルになり、日本以外で海外のメジャーサプライヤーとのビジネスが広がっていいきました。その際に、品質保証部や工場の品質管理部門が、新しいティア1に対して工程品質を確認する際、「トヨタが要求していない項目については開示できない
という課題が一部で出てきました。私たち設計では、これまでは信頼性の評価基準をベースに耐久信頼性を確保するということをしてきました。その一方で、品質保証部や工場品管が、はんだの品質を現場で確認する際、最初に要求しなければいけなくなるケースが増えてきたのです。
そこで2010年に入って以降、品質保証部と私たちが話をして、仕事の仕方を変えてきました。外注設計の部品に関しても、まずは設計から要求仕様を発行し、そのなかで新たにはんだの外観基準も開発時に要求するというプロセスを構築しました。
――その際に作成した基準はどのようなものだったのですか?
トヨタのなかにもインハウスで電子部品を設計して組み立てる工場を持っていたので、そこで使用しているはんだ外観基準をベースに、JISやIPCと見比べながら作成していしました。
しかし、いざ発行してみると、様々なティア1から「この基準はIPCとの関係性はどうなっているのか?」という問い合わせが多くありました。その時に、自動車業界のなかでもIPCがかなりのデファクトスタンダードになっていることを改めて理解し、IPCの610を確認するような形で改訂をすることを検討し始めました。
私たちもなるべく世の中の共通の基準を使っていこうという方針となり、IPC-A-610がAutomotive Addendum(自動車・車載用途向け追加規格)を発行したことに合わせて、2021年2月にIPCベースに切り替えた社内のはんだ外観基準を発行しました。
IPCを取り入れた新しいはんだ外観基準 ティア1からも歓迎の声
――新しいはんだ外観基準の概要と適用範囲を教えてください
基本的には電子部品のはんだ付けとコンフォーマルコーティングの外観基準として適用しています。IPC-A-610では、電子機器のワイヤハーネス等の基準もありますが、そちらは含まない形で運用しています。外観基準とは言っても、BGAボイドなど見えない部分の品質も含んでいて、「はんだ全般の品質基準」という意味で使っています。
――自動車業界も変革期にあるなか、IPCを採用した理由について教えてください
100年に一度の変革期と言われていますが、それ以前からはんだ外観基準については、IPCベースなのか、トヨタ内製がもとになっているか、それともJISを採用しているかで、似た内容や条件でも、受け取られ方がかなり違っていました。グローバル化が進む中で、世界の共通言語としてIPCを使った方が効率的だと判断し、採用を決めました。
IPCが世界の自動車産業でデファクトスダンダードになっており、IECもIPCを元として成り立っていることも大きかったです。
――適用するまでのプロセスで苦労したことはありますか
元々、トヨタ内製で作成していたはんだ外観基準は、私たちの過去の製造経験と信頼性の成り立ちを確認した上での基準になっています。そのため、今回のはんだ外観基準は、「必ずしも100%IPCに適合してください」、という形にはしていません。最上位にある概念は、私たちが要求する、はんだ耐久試験に合致することです。各ティア1でのはんだ付け製造品質は、IPCを基本の共通言語としながら、お互いに確認して決めていきましょうという形にしています。
――IPCを取り入れたことに対して社内外、海外拠点などの反応はどうでしたか?
IPCを核とした新しいトヨタ技術標準を作成して社内に展開し、今はそこから社外へと徐々に伝わって認知されている状況です。主要なティア1取引先からは、IPC基準に沿ったトヨタ技術標準に変えるということに対して、非常に前向きな回答をいただいています。TSCは、ティア1は必要に応じて、要求して頂ければ開示して公開することが可能なので、それを見ていただいて理解して頂く形になっています。
――IPC規格のなかで適用外としたものはありますか?
内製の外観基準とIPCでは一部で差異があった項目は、独自基準を加えて対応しています。実際に適用した結果は、まだティア1からは直接的なフィードバックがないので、今後は、それらを吸い上げながらIPCにも改善提案をしていきたいと考えています。
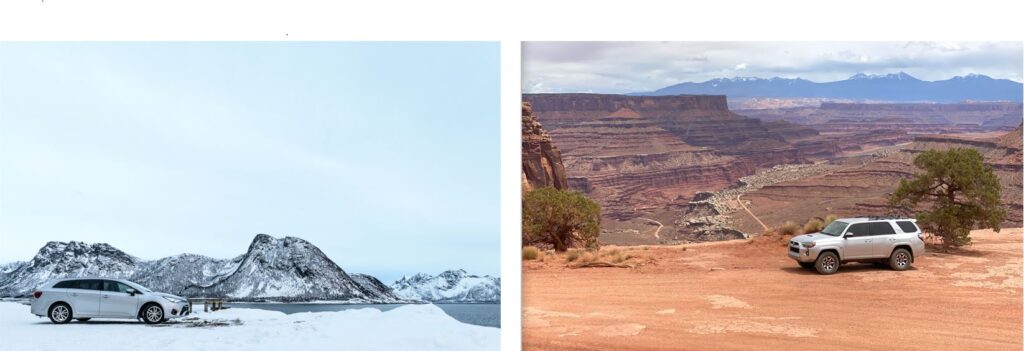
新たな技術標準で効率的な品質管理の実現を目指す
―― IPCを採用するにあたり、標準内容に対しての評価・検証はどのように行いましたか?
元々、社内で使っていた内製のはんだ外観基準とIPCの差分と、関係部署から意見を聞きながら評価検証しました。
最終的な目標は、「弊社のはんだ耐久試験に合致する、はんだ品質基準を決めること
であり、そのためにIPCをうまく活用し、製造品質も効率的に確認できるようにする、という考え方で検証しました。
――トヨタ品質要件とIPC要求条件の違い、差分はどのようなものがありましたか?
例えば、はんだボールでは、IPCでは固定されていれば許容可能という条件になっています。しかし、弊社の車両は、マイナス50℃にもなるロシアや高温多湿下など、様々な環境で長期にわたる使用が想定されています。コーティングだけでの固定では、耐久試験をかけた時、車両使用の最後までコーティングで固定されているかどうかまでは保証していません。そのため、仮に固定が取れたらどうなるかなど、IPCの条件に対する補足をトヨタの技術標準には追記しました。
固定されていればOKというような基準だけでは、基準を守れば良いという考え方になり、チェックリストに○と×をつけて終わる可能性があります。そうならないように、最終的に担保しなければならない製品品質を目標として、これまで通りティア1と相談して合意しながら作っていく形が前提です。
――新たな品質基準を作ったことで国内外のサプライヤーへ期待することは?
グローバルなティア1では、トヨタからは独自の基準を求められ、それ以外のOEMからはIPC基準を求められることがあり、その差異で手間がかかる部分があったのかなと思います。今回トヨタがIPCを採用することで、ティア1サプライヤー様が効率的なはんだの品質管理ができるようになればと思っています。
また、100年に一度の変革期、CASE対応などで、トヨタも従来以上に新しいサプライヤーとお付き合いする可能性が増えてくると思っています。そういう場合に、共通言語としてIPCを使うことで、品質管理の確認を早期かつ効率的に、お互いに行えるようになるのではないかと期待しています。
国際規格への積極的な参加で変化に対応
――2020年、北米で行われたIPC国際標準化委員会にもトヨタ本社から参加いただきました。その時の印象はいかがでしたか。
会議はとてもオープンで、来るもの拒まずの姿勢でやっていることが印象的でした。海外はOEMやティア1、ティア2関係なく積極的に議論を行い、とてもアクティブな会だと感じました。
――日本でもIPC標準化委員会設立に向けて動いています。それに対する期待など
IPCは、メインは海外メーカー主導で運用されています。そこで決まったことがデファクトスタンダードになり、そこからIECとして国際規格になるという流れがあります。
日本のメーカーは品質を現地・現物で確認するという良い文化を持っていますが、それを社内基準として抱え込み、オープンにしたがりません。そのため結果として、後から出てくるIPCやIECの規格に従う構造になってしまっています。内容は社内基準とほとんど同じであっても、違うものを採用しないといけなくなっています。
私たちも自戒を含めて、IPCのように国際的な基準を決めるところに参加し、自らの基準や項目を提案し、後追いにならないようにしていく必要があります。
また、これまで車載の半導体は民生品の10年経ったものを採用するような時系列でした。自動車業界もコネクテッドや自動運転が進み、段々と車載と民生の境目がなくなり、民生品で出た新しいパッケージを採用するようにもなっています。IPCには、そうした新しいパッケージ品に対する品質評価をAutomotive Addendumにも取り込んで頂き、私たちもそれを利用することで効率的に早期の品質確保ができるようにできればと思っています。
もともと半導体パッケージの実装は、日本メーカーが品質的にはリードしていました。それがいまは後追いになっているので、私たちも日本メーカーの協力をいただきながら、IPCに積極的に提案していくことで開発の効率化につながるようにしたいと考えています。
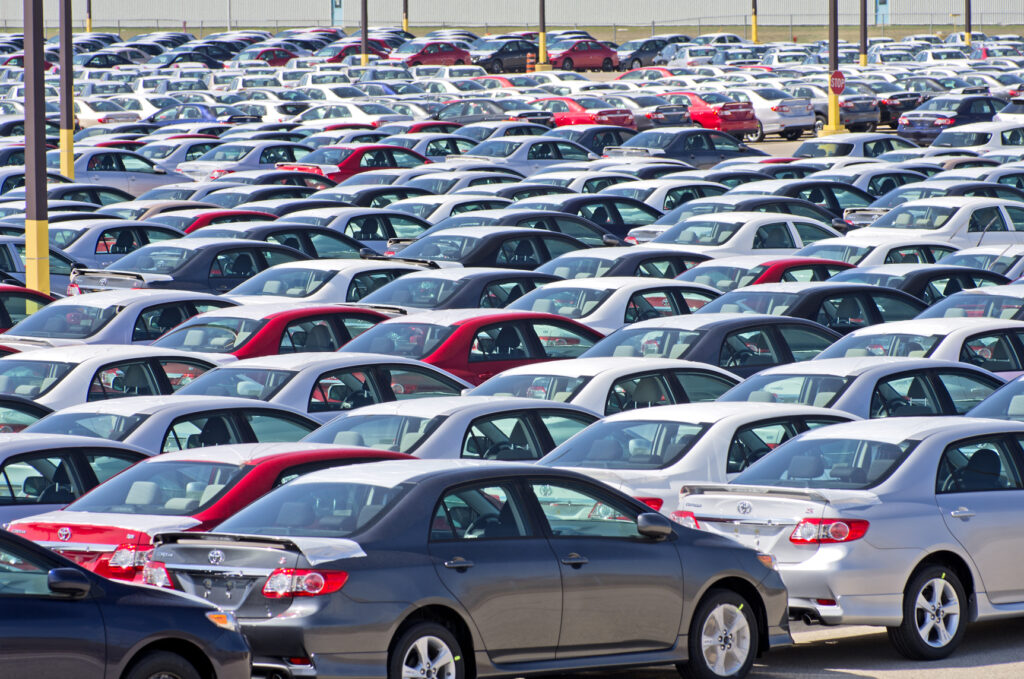
CASEで変わる時代、IPCを共通言語にサプライヤーとの新しい関係を
――日本にはIPCになじみのない企業もまだたくさんあります。最後に今回のまとめと、そうした企業に向けてアドバイスやメッセージなど
トヨタ内製の基準をティア1に展開する時には、IPCとの関係性を質問されることが多々ありました。今回、トヨタとして正式にIPCを採用したことで、サプライヤー様は、グローバルレベルで効率的な製造品質の確認ができるようになります。それが回り回って、私たちにも恩恵があると期待しています。
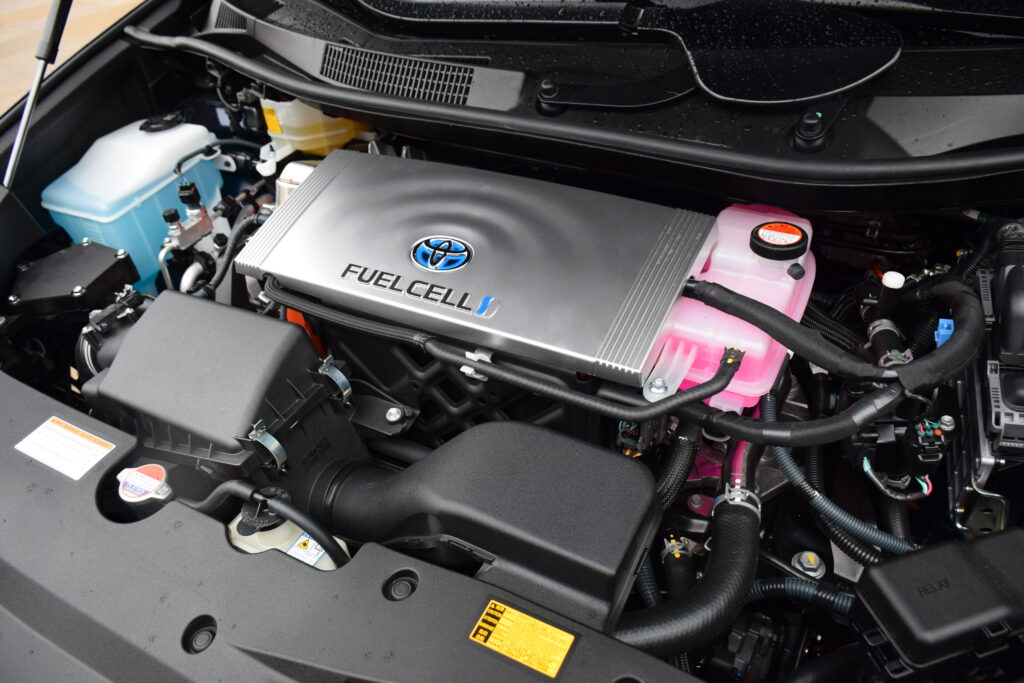
また、これまでは車載部品を作っているサプライヤーや、車載向け半導体を採用してきましたが、これからはその枠がどんどん広がっていきます。私たちも従来お付き合いのなかったティア1、ティア2の企業の方々にもお願いする場合が増えていきます。そこでIPCを活用して頂ければ、その結果として、私たちも効率的な開発や品質確保につながると考えています。
100年に一度の変革期、CASEになり、今までに経験したことがない、私たちの知識と経験だけでは追いつかないような時代になっています。そこで私たちもIPCのグローバルネットワークの仲間に入ることで、最新情報を取り入れながら、様々な技術をトヨタ車に実装できるようにしていきたいですね。