前回の記事ではDXにおけるデータドリブンの重要性について解説しました。今回はその前段にあたり、「そもそもデータを集めるべき工程をどうやって見つけたら良いのか?」という疑問に答えていきたいと思います。
企業におけるDXは大きく分けて以下の6つの流れで説明できます。
- 自社の現在地を知る ②DXビジョンを作成する ③作業工程を可視化する ④プロセスを考える ⑤DX推進チームを立ち上げる ⑥デジタル改善を実行する
補助金などが使えるケースもあるため、いきなり⑥から着手しデジタルツールをとりあえず導入する中小企業も多いです。しかし目的がはっきりしないまま導入を進めれば結局、使っていないもしくは使い切れていないという事態に陥ります。
今回は④の「プロセスを考える」という項目について深掘りします。自社の製造・業務プロセスを洗いざらい言語化し、どこに改善の余地やムダがあるのかを見つけやすくする「プロセスアプローチ」の作業です。
このプロセスアプローチは2つの手法に大別できます。まず「タートルチャート」の作成。ある作業工程について、前の工程から受け取る段階を「インプット」、そして次の工程に渡す段階を「アウトプット」と定義します。
例えば制御盤では複数の部品を取り付け、次にそれらを配線でつなぐという生産の流れがあります。部品が運ばれてくるのが「インプット」、そして部品を取り付けたものを次の配線工程に渡すのが「アウトプット」となります。
製造業ではモノと情報の流れがインプット・アウトプットを繰り返して製品ができていくはずです。このインプットとアウトプットのコミュニケーション部分に、改善できるチャンスが眠っていることが多々あるのです。
これは分かりやすすぎる例かもしれませんが、組み立て作業に必要な図面をプリントアウトして次の工程に渡している現場を想定しましょう。これをPDFにするだけでも修正・変更依頼がしやすくなり、ムダな作業時間やリソースを減らすことができます。
それぞれの作業工程での効率化はすでに尽くされているケースが多いです。いったんアウトプットすると俯瞰するのが難しくなり、組織全体でみるとまだまだ足りないところがあるのを見落としてしまいます。インプットとアウトプットの整理はそれをチェックするのに役立ちます。
作業工程そのものについても、どれだけのリソースを投じているか分解します。
- 人的資源(作業員、検査員、出荷担当の人数)②物的資源(製造機械、検査機器、梱包機の台数)③方法(マニュアル、手順書、検査基準の数)④測定(不良品率、生産数、納品日数)と大きく4つのカテゴリーで計12種類に分けて書き出します。
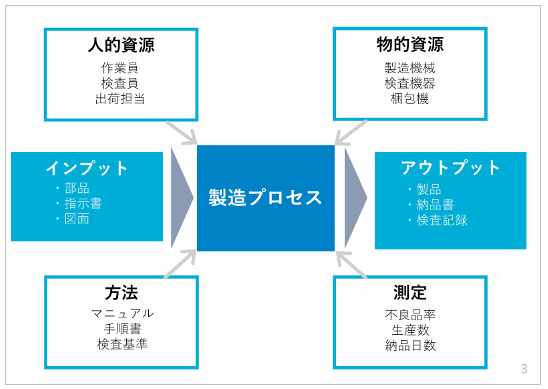
タートルチャートで見える化した投入リソースのうち、改善すべきものやデジタル化できるものの基準を明確にします。東洋電装ではチャート内の項目すべてを改善の対象にしています。作業のマニュアルや手順書がアナログでも、現場で作業する方々には「そういうものだから仕方ない」という空気がありました。しかし実際には過去の実績データを見られるアプリを開発したことで、次の案件の見積もりや作業効率を飛躍的に高めることに成功しました。
次にプロセスアプローチの2つ目です。業務フローを徹底的に分解し、チャート図を描きます。思った以上に泥臭くて手間がかかりますが、取り組む価値があると言い切れる作業です。
まずは会社の活動を受注や生産、納品などおおざっぱに分けます。その後、もう少し細かい内容に区切ります。「受注プロセス」という大カテゴリーのなかに「見積価格の決定」「部品の選定・確認」「実際の受注決定」などの業務フローが中カテゴリーとして入るイメージです。
中カテゴリーをさらに細かく解剖していきます。「見積価格の決定」という行為のなかだけでも、以下のような仕事があります。
見積もり依頼を顧客から受ける→材料価格を概算する(必要があれば見積もりを取る)→納期内に対応できるか検討する→外注先リストを確認して適正な外注を選定する→概算価格を見積もる→決裁文書(システム)に入力して印刷する→A課長のハンコをもらう→文書をスキャンして顧客にメールで送る。ここまで細かく追います。
そうすると「なぜ文書を印刷しているのか」など非効率な部分や、「A課長」など個人に頼っている業務が明らかになります。これではA課長がいないだけで見積価格を出すのが遅れます。チャート図にすることで、他部門の社員の目からも指摘を受けやすくなります。
東洋電装でも制御盤の部品在庫が一部なくなった際の動き方について業務フローをまとめました。制御盤は100点以上の部品で構成され、多くの在庫を抱えて生産しています。代理店の状況によっては、どうしても特定の部品を切らしてしまうことがあります。
まず組み立て職人が部品の在庫切れに気づくと、部品棚を探します。それでも見つからなければ購買部門に確認します。購買の担当者はシステムを調べます。それでもなければ職人は在庫がない部品を後回しにし、他の部品の取り付けを始めます。
ここではまず、職人が部品棚や購買に行く時間はムダです。入荷や手配ステータスを職人が直接見られるような簡易的なシステムを作りました。
ここまでは対処療法で、ここで終わってはいけないというのが業務フロー作成の真髄です。明らかになった課題をもとに、データを使ってさらにどんな改善ができるのかを考えるのが重要です。
たとえば未入荷の部品情報から作業工程の変更をAIが提案してくれるようにする、よく欠品する部品については在庫を増やすことでロスを減らす、などがあります。
問題のある業務フローの影には、もっと根深い課題が潜んでいます。データドリブンでさらなる仮説を立てて、動き出すことが欠かせないのです。自然とこの思考が身につけば、製造業におけるDX人材としては優秀です。
東洋電装がこうした業務フローの作成についてコンサルティングサービスを手掛けているからというわけではないのですが、チャート図については第三者を入れてつくるべきです。
社内だけでやろうとすると聖域や既得権益の概念が強まり、思うように進まないことがあるからです。「自分だけがこの業務を担当している」というのは存在意義に直結しており、なかなか実態を社内全体にオープンにしようという考えが生まれにくいのです。
【著者】
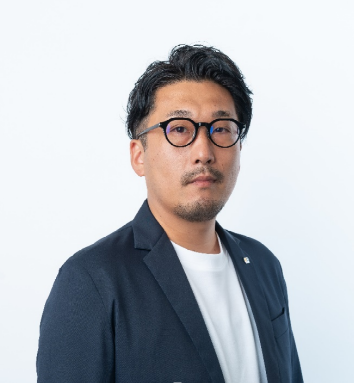
越智 稔(おち みのる)
東洋電装株式会社
制御盤システム事業 事業部長
1984年愛媛県生まれ。制御盤の設計としてキャリアをスタートし、13年間エンジニアとして国内向けだけでなく海外向けのプラント関係制御設計及びシステム開発経験がある。PLC-HMI-SCADAの開発経験も多く、ロックウェル・オートメーションやシーメンスの開発経験と複数カ国の現地でのコミッショニングを経て技術力を高めた。更に欧州向けのIEC60204-1に準拠した設計によるCEマーク取得パネル、UL508Aに準拠したUL認証パネル設計を多く行った経験がある。現在は制御盤製造の事業運営と自社DX推進及び中小製造業のDX推進をサポートする新規事業を産官学連携で立ち上げ、システム開発統括及びフィールドサポートを行っている。